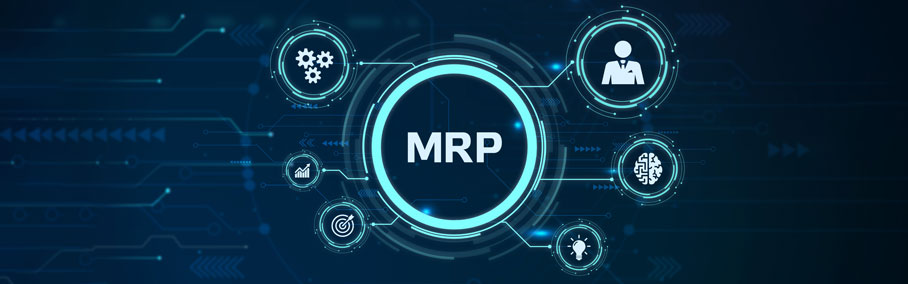
“The Big Three” of MRP. Material Requirements Planning
MRP – Opening the Black Box
Material Requirements Planning can seem like a mystery on how it does its magic behind the scenes. Let’s consider how you can help it work more efficiently and understand why it’s giving you the data it does.
MRP is based on “The Big Three.” No, not the “Big Three” automakers, the other “Big Three:”
- Requirements
- Inventory
- Replenishments
We take the data from “The Big Three” and add tools to make calculations.
The single most important tool is a calendar. We also need “Planning Data” about the parts for which we are going to plan.
- Minimum Purchase Order/Job Quantity
- Standard Purchase Order/Job Quantity
- Minimum Inventory Quantity
- Maximum Inventory Quantity
- Lead Time (Purchase or Job)
If we were going to manually calculate MRP, we would use a spreadsheet that may look something like this:
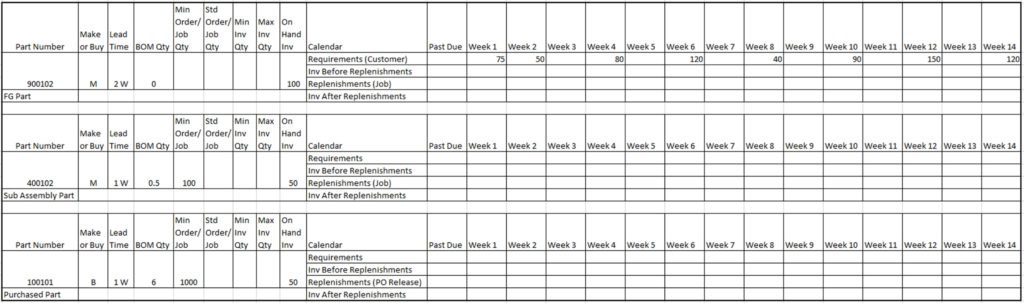
This is a simple structure with a Finished Goods Part at the Top. It has one subassembly in the middle and we’re only listing one purchased part at the bottom.
We have some Customer Requirements listed but no calculations have been added.
Let’s take a look at the calculations.

Week one – Inventory starts at 100 EA; we have requirements of 75 EA. (100-75=25)
Simple so far. No job is required since we still have inventory in stock.

Week two – 900102 Inventory starts at 25 EA; we have requirements of 50 EA. (25-50=-25)
The calculation is still simple.
What happens to the job we need to build more 900102?
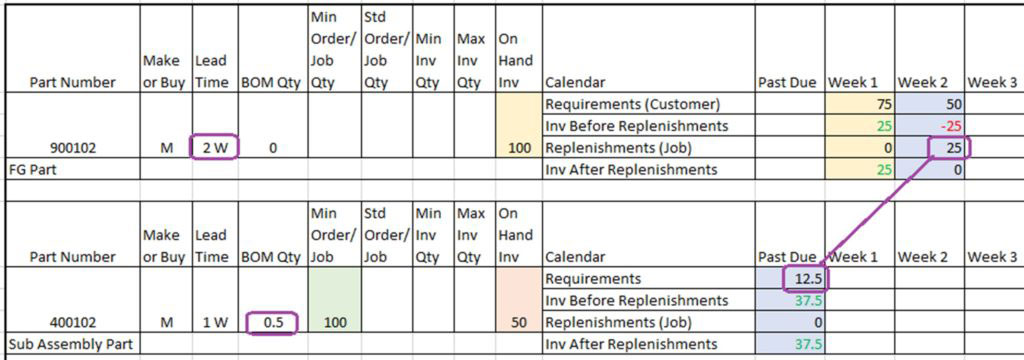
The 25 EA Job (Replenishment) of 900102 becomes the requirement for the sub-assembly 400102.
900102 also has a lead time to build the parts of two weeks. We only use 0.5 (BOM Qty) of a 400102 to make each 900102, so the requirement is for half of the job for 25 EA at 12.5
That is why we show the requirement (Job Start Date) for 400102 – two weeks before the job is to be completed.
400102 Inventory starts at 50 EA; we have requirements of 12.5 EA. (50-12.5=37.5)
So, everything is going well so far.
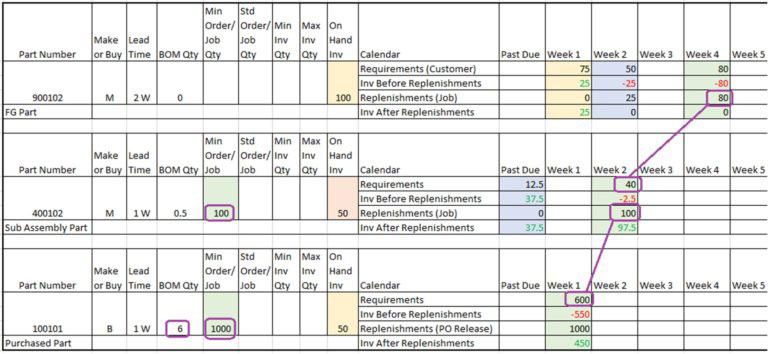
Week three – no activity
Week four – 900102 Inventory starts at 0 EA, we have requirements of 80 EA
Open a Job for 80 EA of 900102.
400102 Inventory starts at 37.5 EA; we have requirements of 40 EA (0.5x BOM Qty)
Open a Job for 100 EA of 400102. The minimum job quantity is 100 EA (that’s why…)
100101 Inventory starts at 50 EA; we have requirements of 600 EA (6x BOM Qty)
Enter a PO Release for 1000 EA (Supplier has a policy to sell a minimum of 1000 EA)
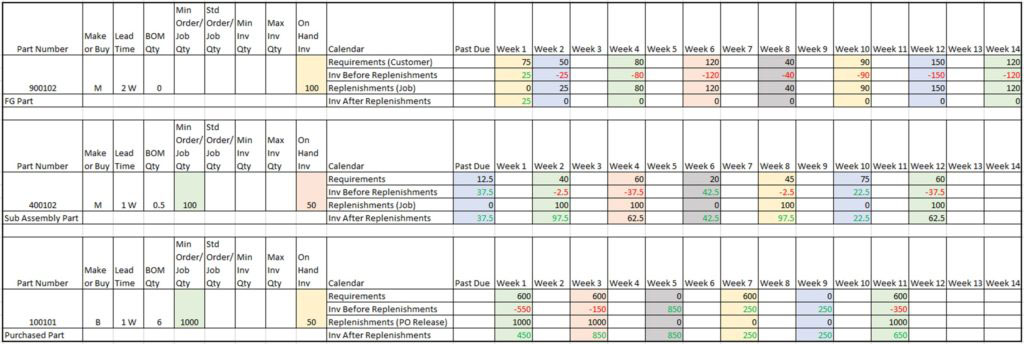
All weeks are planned and ready to go.
The other planning data values (Standard Order/Job Quantity, Minimum Inventory Quantity, Maximum Inventory Quantity, etc.) will each impact the calculation as they are applied.
Now, you can show your boss exactly why you ordered 1000 EA of the purchased part. You won’t have to say, “The system said to do it.”
You will be the MRP wizard!