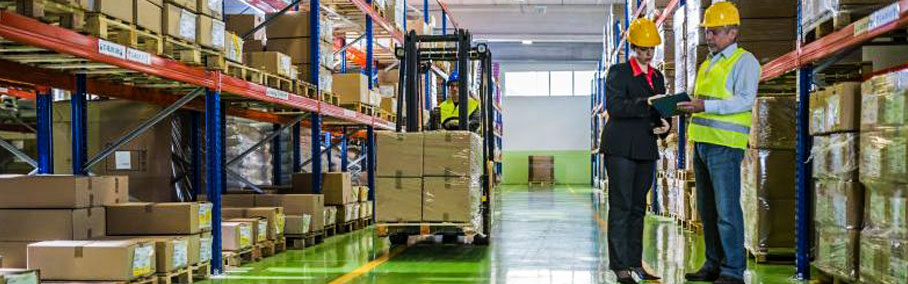
How to Improve Inventory Accuracy on the Production Floor
Do you feel as though the production floor is your worst enemy in the mission for inventory accuracy? This leading cause of frustration and stress around inventory management often comes from a lack of investment and standards on production floors. Inaccurate inventory impacts the ability to deliver customers their parts, borrow money for capital and raw material needs, and produce profits. The lack of investment in the tools, training, and work place standards on the production floor are all root-causes of an inability to sustain inventory accuracy. Investments must be made into people, processes, and procedures.
The three key focus areas:
Everything should be in its place and marked
Inventory, (including raw material, MRO items, and finished goods) have a cash value. No matter if they reside in warehouses or at machines, locations should be clearly marked, clean, and accessible. Inventory should always be properly labeled and valued. Effective organization and marking of the facilities will ensure that every piece of inventory has a home and can easily be found.
Define, Implement, and Sustain Standards by:
- Adopting workplace organization methods (Like 5S).
- Developing Audit Programs to insure standards are maintained.
- Involving operators and material handlers in workplace layouts.
Invest in Mobile Hardware & Barcoding
Effective and modern ERP systems provide robust mobile functionality. This allows material handlers and managers the ability to scan inventory identification tags to obtain information on the locations the inventory is being moved to/from. If the current system requires a trip back to a PC terminal to manually key in the data, the room for error can double and even triple. Mobile inventory transactions performed at the point of use, are far more effective and efficient. Investing in tablets, barcode readers, printers, mobile PCs, and Wi-fi improves the efficiency of inventory transactions and reduces the excuses and errors in maintaining accurate inventory.
Areas where mobile hardware should be considered are:
- Receiving
- Warehouses & Tool Cribs
- Workcenters
- Material Handling (Including Forklifts)
- Shipping
Verify Training Effectiveness
In today’s environment of continuous improvement and growing workforces, training on the production floor is critical to producing results. We should avoid “one-way fits all” training methods and programs. Employees learn differently. Some people can grasp concepts from a conference room, while others require hands-on effort in the work environment. No matter how in-depth the training and related documents are, it is imperative that leaders verify how effective the training was. This verification can be done by developing an ongoing auditing plan to verify that the actual transactions on the production floor and warehouses are being performed accurately. These efforts will help to identify processes and employees which require additional training and attention.
Keys to a successful Training Program are:
- Processes Documented with flow-charts and screen captures.
- Ongoing Effectiveness Auditing.
- Avoiding one-way/size fits all training methods.
By focusing on the production floor through developing workplace standards, investing in point of use hardware, and improving training effectiveness, a plant can and will produce sustainable inventory accuracy throughout the production process.
If the time, skills and talent to develop, implement, and sustain these industry best practices are not available within the organization, management should look outside of the organization to consultants and coaches who can train and mentor the leaderships teams on the path toward world-class.
As organizations develop these new standards and disciplines on the production floor, they will realize a return on our investment through improved on-time delivery to customers, increased capacity, and sustainable bottom-line improvements to P&L Statements.